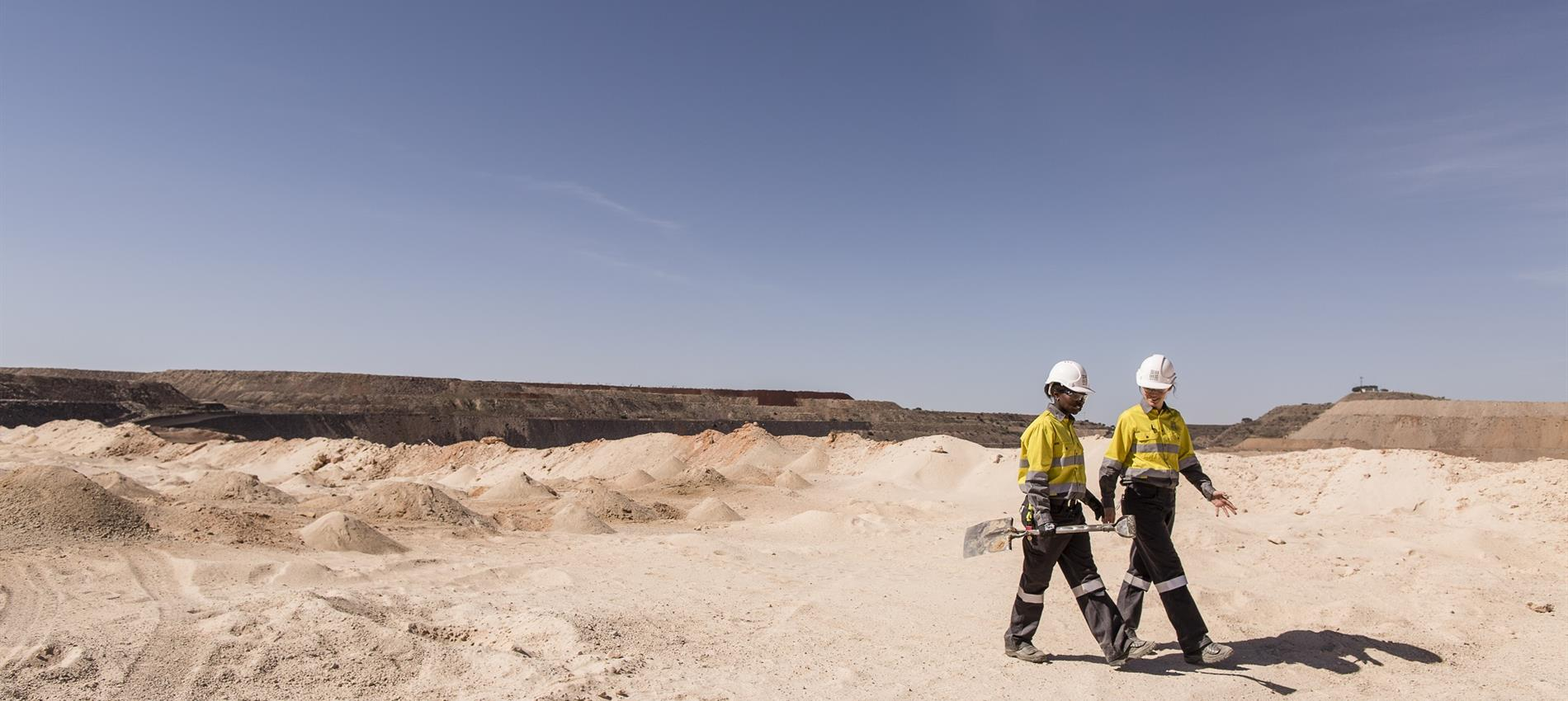
Manganese ore
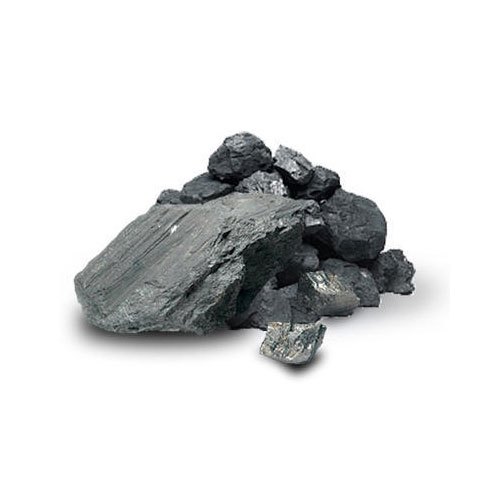
Steel becomes harder when it is alloyed with manganese. It has similar applications when alloyed with aluminum and copper. Hardened steel is important in the manufacture of construction materials like I-beams (24% of manganese consumption), machinery (14% of manganese consumption), and transportation (13% of manganese consumption)
Magnese ore offer
- High concentration
- The ore grade is from 42-47% purity
- Supply capacity 1,000 tonns per month
- Price: make your inquiry office@metaltrade.fi
Introduction
Most manganese (in the form of manganese ore and manganese alloys) is used in metallurgical processes and around 90% of mined manganese ores and the resulting alloys are used in steel production, with ferromanganese mostly used to improve the hardness and wear resistance of steel and silicomanganese used to give steel increased strength and function. Manganese is also used to remove sulphur and oxygen from steel. Approximately 6-9 kilograms of manganese are required to produce a tonne of steel and there are no viable substitutes for manganese in the conversion of iron ore to steel (meaning that steel cannot be produced without manganese). In the automotive sector, steel is used throughout the car, including the body structure, drive train, suspension, wheels and braking system. An average car contains approximately 900 kg of steel, which equates to 5-8 kilograms of manganese in each vehicle.
Manganese is the twelfth most abundant metal, with an average concentration of around 1,000 parts per million in the Earth's crust. However, its uneven distribution means it is only rarely found in high enough concentrations to be suitable for mining. Consequently, manganese production is highly concentrated, with South Africa, Australia and Gabon delivering approximately 60% of the global supply. South Africa alone is responsible for approximately one-third of global production and holds around 75% of currently identified resources.
In addition to terrestrial manganese, substantial resources exist on the seabed in the form of ferromanganese nodules and crusts. These may exceed land-based resources, but have not been commercially exploited due to a range of political, legal, economic, technical and environmental challenges that still need to be resolved. Ultimately, it may be the presence of other critical metals in seabed nodules and crusts (such as rare earth elements, cobalt and nickel) rather than the more common manganese that drives development of seabed mining as a commercial reality.
Manganese ore mining is a mechanised large-scale activity, with most deposits shallow enough to extract using open pit mining methods, with only few large operations employing underground methods. In both open pit and underground mines, the manganese ore is extracted using drilling and blasting. Dependent on the grade of the ore extracted, it may be transferred to a beneficiation plant to be upgraded or (more rarely) shipped directly to purchasers with little or no further processing.
Manganese ore is the primary source of manganese used in the manufacture of manganese ferroalloys. To be used in this way, most as-mined manganese ore is upgraded by beneficiation, which comprises first crushing and milling (to physically separate valuable and non-valuable minerals) and then concentration (to selectively recover the valuable manganese mineral). The target manganese content for the concentrate produced by beneficiation is normally in the range of approximately 38-55%, if destined for use in metallurgical processes. Depending on the grade of the as-mined ore, beneficiation can generate large volumes of fine waste (known as tailings), which must be disposed of and managed carefully to avoid the risk of long-term environmental impacts and sudden catastrophic releases.
The key manganese ferroalloys are ferromanganese and silicomanganese, which are produced from manganese concentrate and differing amounts of carbon, iron and/or silicon in high temperature processes. To ensure the process is efficient, the fine concentrate from beneficiation must be formed into coarser pellets with suitable physical characteristics as a feed material.
Manganese is recycled principally as a constituent of ferrous and non-ferrous scrap, but is not the specific target of recycling. Recycling methods for rechargeable batteries currently being piloted are likely to be commercially developed as battery use in electric vehicles and energy storage systems continue to rise, allowing the manganese content (and other metals) to be recovered and returned to productive use (rather than being disposed of in landfill as a hazardous waste as has historically been the case). Waste slags from ferromanganese and silicomanganese production that contain significant residual manganese can be reprocessed to use or recover some of that manganese.
What are manganese ore used for?
Most of the manganese produced is used in the form of ferromanganese and silicomanganese alloys for iron and steel manufacture. Manganese ores containing iron oxides are first reduced in blast furnaces or electric furnaces with carbon to yield ferromanganese, which in turn is used in steelmaking.
What are the uses of manganese?
- It is an important raw material in the iron and steel industry as it is used for hardening steel and prevents it from rusting.
- It is used in dry cell batteries.
- It is used in forming many alloys.
- It is used in chemical, glass and electrical industries.
Manganese ore reserves by region, 2021
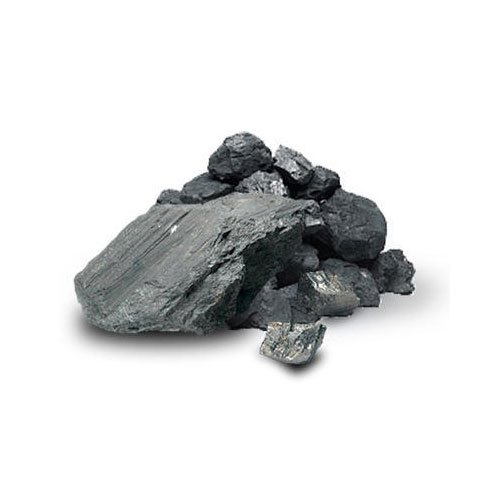